EDM AND
EROSION
Filigree components.
Eroded with high-precision.
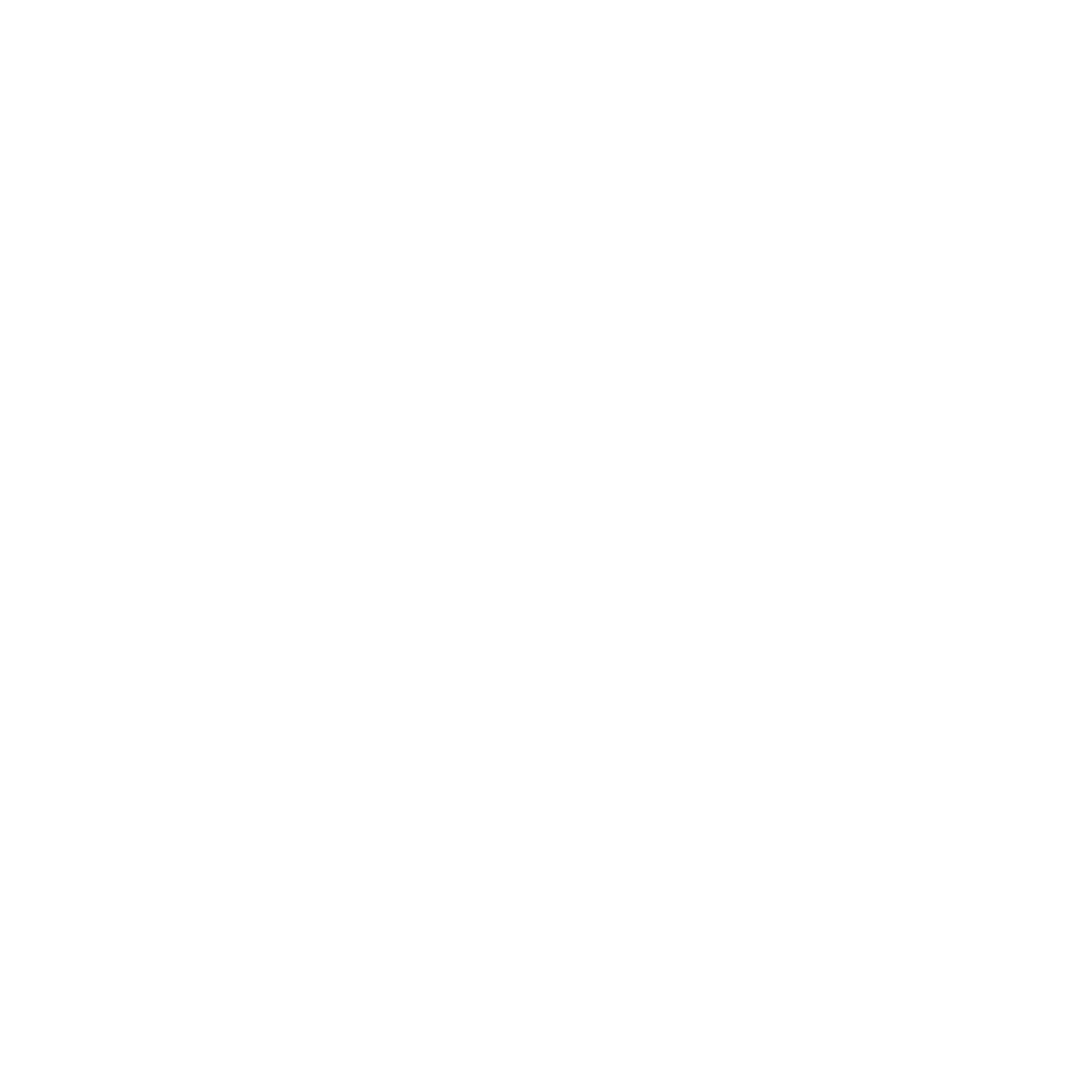
Where other technologies reach their limits due to complex geometries and material properties, electric discharge machining – or EDM for short – can score with outstanding dimensional accuracy and surface qualities.
We produce the finest contours, cuts and corner radii using EDM technology. Depending on the component requirements, we use two processes: wire erosion and EDM. With both technologies, we process electrically conductive materials, regardless of their hardness, with the highest precision.
Your advantages at a glance
- Precise erosion of filigree geometries
- High capacity and productivity
- Unbeatable employee expertise in machining technology as a result of decades of experience
- Flexible and fast machining times
- Quality assurance for a dimensional accuracy of up to 0.3 µm
- 100 % air-conditioned production and assembly infrastructure
- Documentation of all dimensions and geometric tolerances
- Reproducible quality
- Certified in accordance with EN 9100:2018, including ISO 9001
Wire erosion
We manufacture extremely complex geometric shapes using the latest generation of wire erosion machines. Using erosion wires with wire diameters of 0.1 to 0.25 mm, we wire erode with an accuracy of ± 0.003 mm with surface qualities of up to Ra 0.1 – 0.2 and with the smallest corner radius of 0.07 mm.
An additional dividing head on our Agie Charmilles CUT 200 mS enables us to produce offset contours. The additional rotary axis results in an increased level of automation for cost-efficient component production.
Wire erosion – how it works
In wire erosion technology, the contour of the precision part to be machined is melted off with high precision using the finest brass wire. A spark forms between the erosion wire and the workpiece and it removes the material from the workpiece to be machined. The process takes place in a medium with a defined conductance (deionised water, synthetic oil).
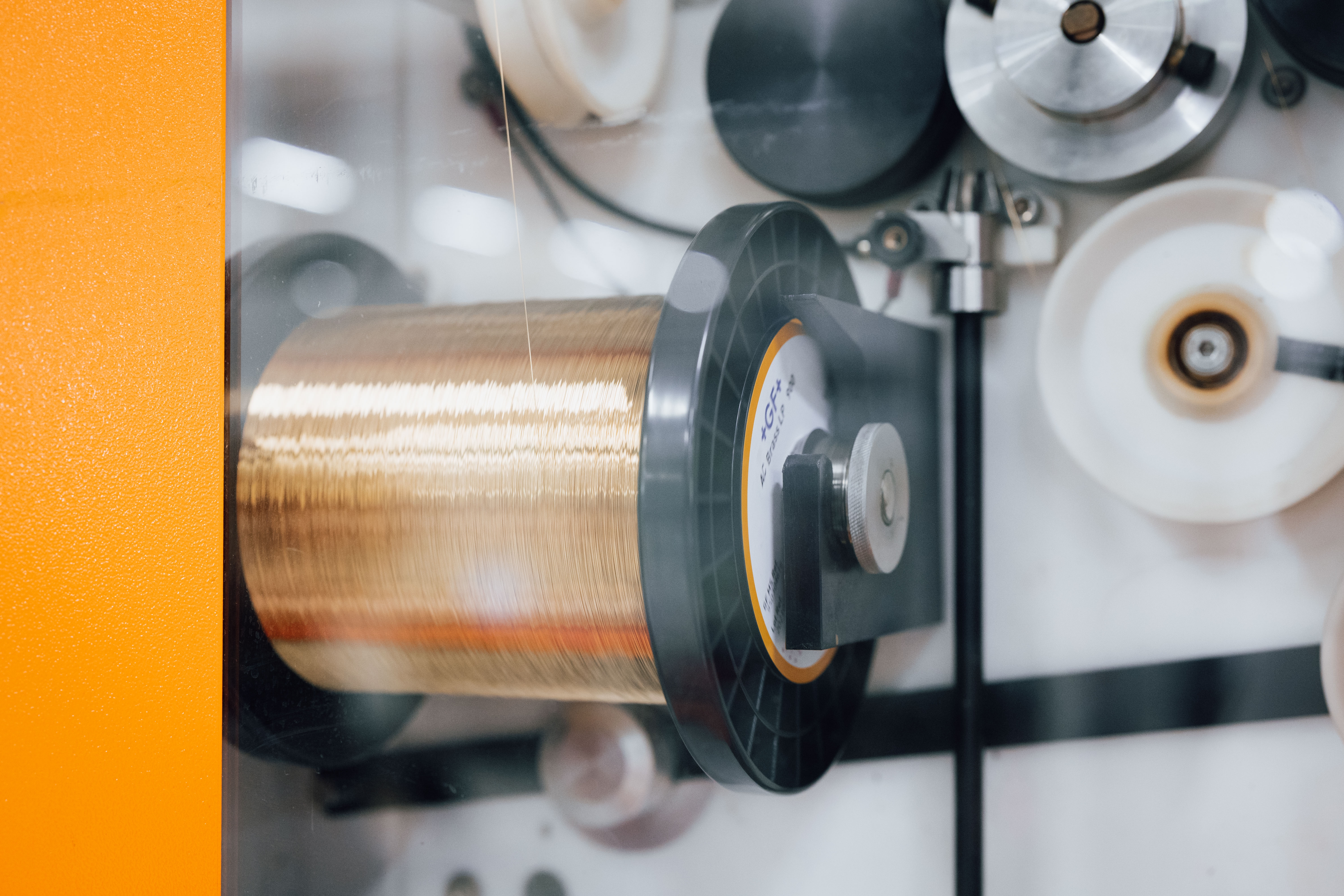
Machining options
- Maximum machining size 550 x 350 x 400 mm
- Maximum achievable surface roughness: Ra 0,1 – 0,2
- Wire diameter between 0,1 and 0,25 mm
- Smallest possible corner radius of 0.07 mm
Application
- Prototype machining
- Single part production
- Small-batch production
EDM
Our automated EDM machines are designed for a variety of applications and have many machining functions. This ensures short cycle times and a flexible application when manufacturing individual parts. For small series, an automation system enables 24/7 operation.
EDM – how it works
EDM is also an erosion process, in which the shape of the workpieces to be machined is produced by an electrode. In EDM, the electrode represents the counterpart of the planned workpiece shape. The removal takes place in an electrically non-conductive – dielectric – fluid. The electrode and the workpiece are placed in a dielectric bath.
During EDM, there is no mechanical contact between the workpiece and the electrode at any point in time.
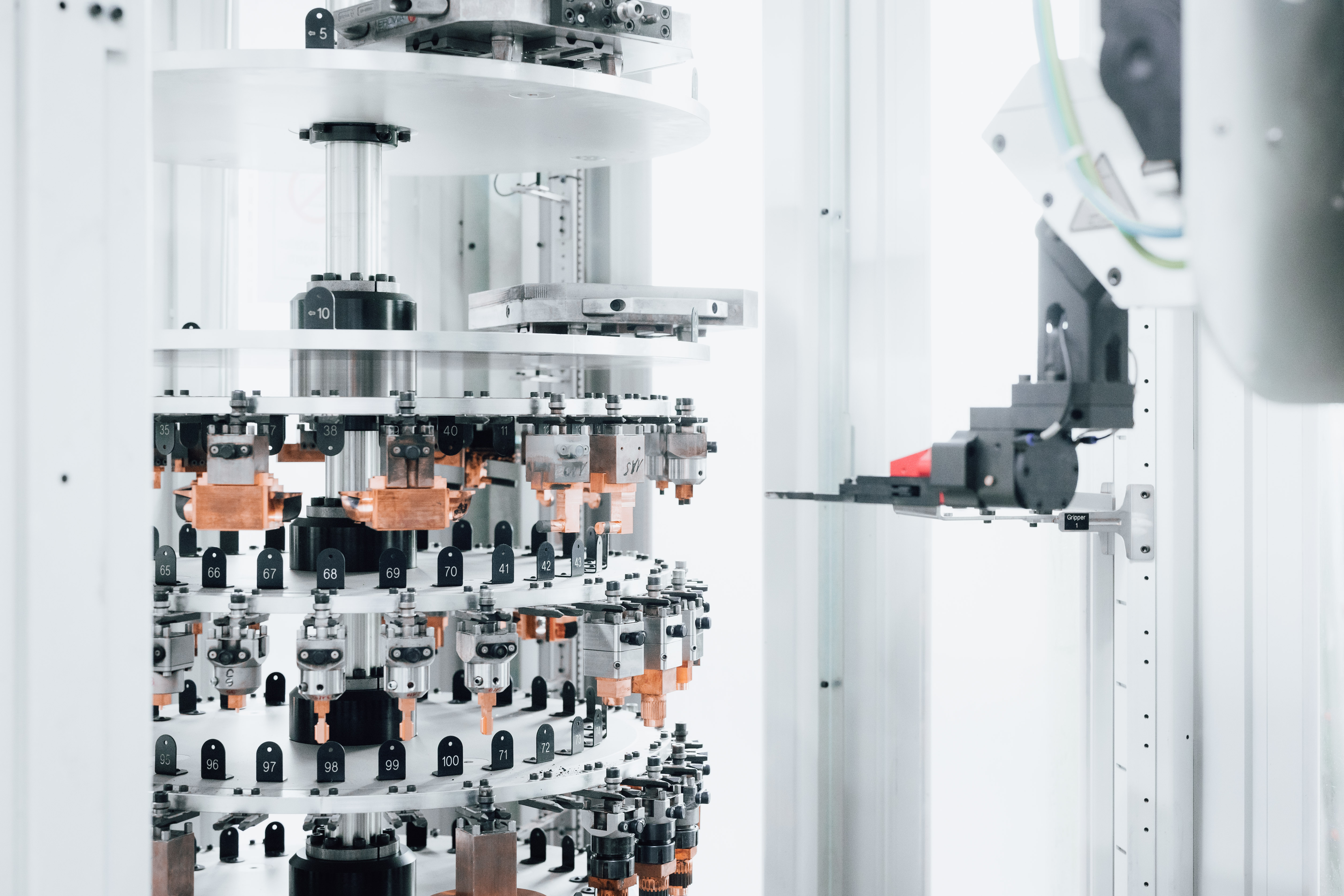
Machining options
- Maximum machining size 600 x 400 x 500 mm
- Maximum achievable surface roughness: Ra 0,1 – 0,2
Application
- Prototype machining
- Single part production
- Small-batch production
Materials
- Hard metal
- PM steels
Infrastructure
We work with erosion machines of the latest generations:
- 3 EDM machines, incl. robot system
- 5 multi-axis wire erosion machines
- 1 starting hole drill
Component finishing
We reliably meet additional requirements for dimensional and surface tolerances with sophisticated grinding technology.
Edge technologies
We handle surface treatment, heat treatment, welding, sheet metal forming and additive manufacturing with the help of specialised, certified partner companies.
SK TECHNOLOGY 4.0
Using transparent, digital precision technology, we master the most complex requirements in precision technology with the highest quality standards and ambitious delivery times.
We can also do filigree.
See for yourself!
Get in touch with us now:
TEAM PROJECT MANAGEMENT
Phone +49 (0) 9461 91106 – 0
E-Mail info@sktechnology.de
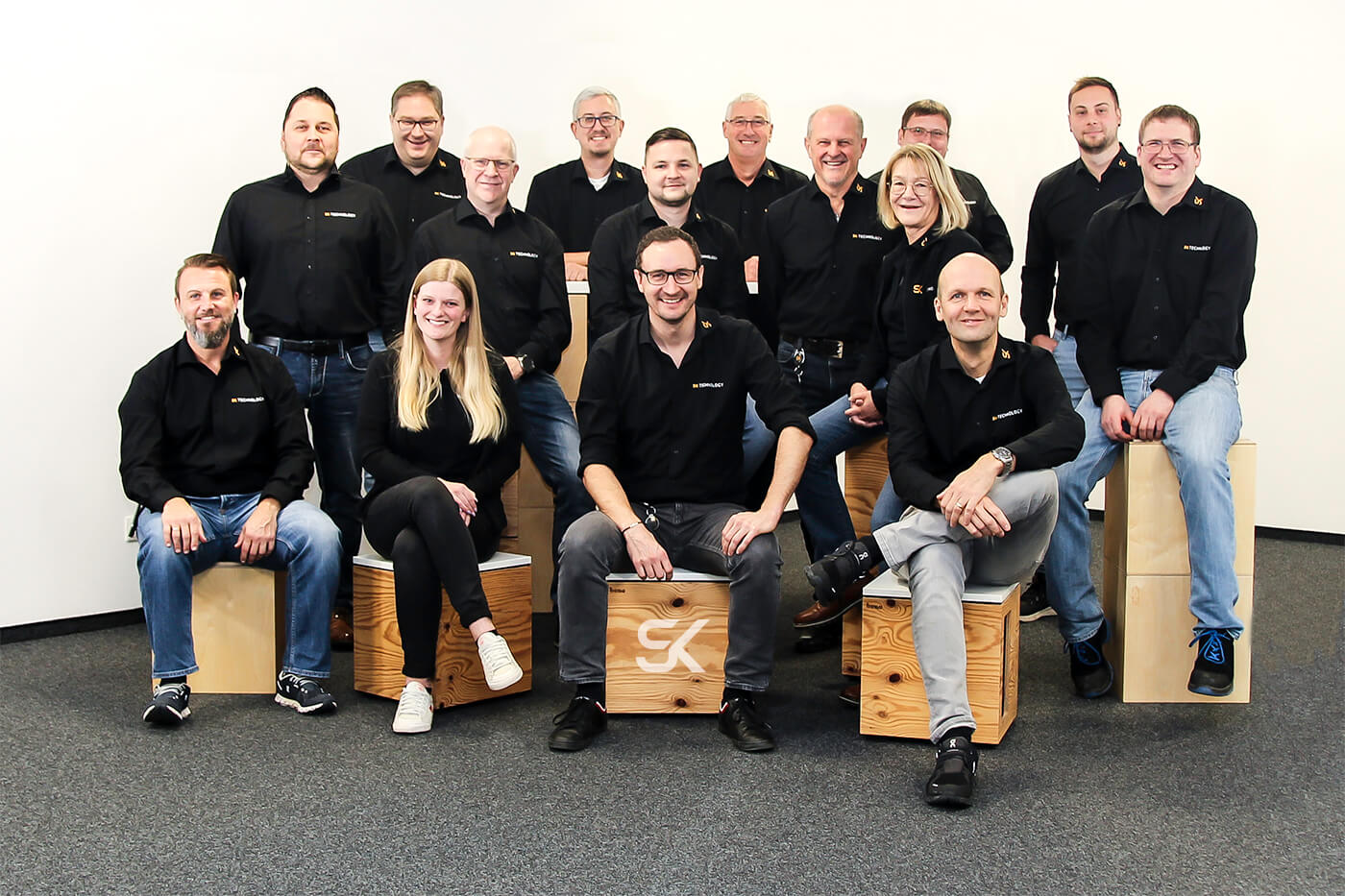